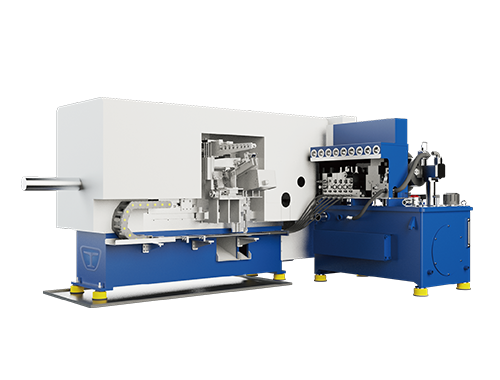
Огляд
Запит
Суміжні продукти
Вступ
Інерційна фрикційна сварка - це сучасний процес твердого стану сварки, який широко визнано завдяки своїй високій якості, ефективності, економії енергії та безшкодності для середовища. Вона має широкі перспективи застосування у галузях, таких як авіакосмічна, автомобільна промисловість та добыча нефтяних скважин, і отримала значну увагу від країн з розвиненою промисловістю.
Процес инерційного фрикційного з'єднання включає утримування обертального кінця робочого елемента у літаку. Процес зварювання починається із прискорення літака та обертального кінця робочого елемента до певної швидкості, після чого літак від'єднується від головного мотора. У той самий час, рухомий кінець робочого елемента продувається вперед. Коли робочі елементи зустрічаються, генерується тертя тепла. Під час цього процесу літак зупиняється через момент тертя, його швидкість зменшується. Коли швидкості літака, валової системи та обертальної щипців з робочим елементом спадають до нуля, температурний розподіл у зоні стыку досягає необхідного рівня. Нарешті, під дією осьового тиску, процес зварювання завершується.
Параметри процесу інерційного фрictційного зварювання включають три головні фактори: обертовий момент маховика, швидкість маховика та осьова тисня. Їхні головні характеристики — стале тиснення та змінна швидкість, що поєднують процеси нагріву та ковки неперервного фрictційного зварювання.
Специфікація параметрів
Максимальна сила ковки: | 60кН |
Діаметр зварюваного прутка: | 5-12мм |
Вращальний фіксатор : | 50-150мм |
Швидкість валу : | 2500-3000об/хв |
Ход слайду : | 200мм (діаметр) |
Рух : | довжина пристрою 50-400КВт |
Ефективність виробництва (час зварювання): | 4s |